- Determine the Chemical Composition and Tensile Strength of the Base Metal
- Select Filler Metals Options Relative to the Welding Process
- Determine the Right Welding Process for your Project
- How to Read the Welding Electrode Designation Format
Getting this wrong could be tragic under any welding code including ASME Section IX’s Boiler and Pressure Vessel Code, AWS D1.1 – Structural Code, API 1104 - Pipeline Code and so on.
Not matching the base and filler metal correctly can cause a reduction in the overall tensile strength of the materials, reduce load bearing capabilities and could ultimately lead to catastrophic disasters. However, there are four key steps that could be taken to help accurately match the filler metal to the base metal.
Step 1. Determine Chemical Composition and Tensile Strength of the Base Metal
It is imperative when matching filler metal to base metal that the filler metal is compatible with the base metal’s chemical composition and tensile strength. This information should be used to match chemical properties and determine the strength of the structure being welded, e.g., welding Base Metals with tensile strength of 60,000 psi will require Electrodes of the same or greater tensile strength to maintain the strength of the base metal, e.g. E6010 or E7018 may be perfect in this case for welding and maintaining the strength. Whether it’s a pressure containing vessel or a load bearing structure, this information provides the resistance in which a material will break under tension.
Step 2. Determine the Welding Process
Knowing the welding process that will be used to weld the metals together, dramatically reduces the number of filler metal options. This reduction is shown in the AWS’s Filler Metal Specifications chart. This chart shows the grouping of filler metals that have similar chemical properties into the same specification and denotes the spec with an A/SFA Number.
The AWS also charts these specs by Material and Welding Process shown below in the “AWS Filler Metal Specifications by Material and Welding Process” this chart shows the reduction of possible filler metals per process and per material being used.
AWS Filler Metal Specifications by Material and Welding Process |
OFW | SMAW | GTAW GMAW PAW | FCAW | SAW | ESW | EGW | Brazing | |
Carbon Steel | A5.2 | A5.1 | A5.18, A5.36 | A5.36 | A5.17 | A5.25 | A5.26 | A5.8, A5.31 |
Low-Alloy Steel | A5.2 | A5.5 | A5.28, A5.36 | A5.36 | A5.23 | A5.25 | A5.26 | A5.8, A5.31 |
Stainless Steel | A5.4 | A5.9, A5.22 | A5.22 | A5.9 | A5.9 | A5.9 | A5.8, A5.31 | |
Cast Iron | A5.15 | A5.15 | A5.15 | A5.15 | A5.8, A5.31 | |||
Nickel Alloys | A5.11 | A5.14 | A5.34 | A5.14 | A5.14 | A5.8, A5.31 | ||
Aluminum Alloys | A5.3 | A5.10 | A5.8, A5.31 | |||||
Copper Alloys | A5.6 | A5.7 | A5.8, A5.31 | |||||
Titanium Alloys | A5.16 | A5.8, A5.31 | ||||||
Zirconium Alloys | A5.24 | A5.8, A5.31 | ||||||
Magnesium Alloys | A5.19 | A5.8, A5.31 | ||||||
Tungsten Electrodes | A5.12 | |||||||
Brazing Alloys and Fluxes | A5.8, A5.31 | |||||||
Surfacing Alloys | A5.21 | A5.13 | A5.21 | A5.21 | A5.21 | |||
Consumable Inserts | A5.30 | |||||||
Shielding Gases | A5.32 | A5.32 | A5.32 |
Step 3. Determine the Welding Position
Welding Position is another critical variable when selecting the appropriate filler metal. Some filler materials are molten and are so fluid that using the electrode in certain positions such as vertical or overhead can lead to harm of the welder and prevent complete joint penetration of the weld due to the positioning of the materials being joined together.
Grove Welds
Below are example welding positions for groove welds (plate and pipes) and also fillet welds (plate) positions.
Step 4. How to Identify the Right Welding Electrode
When selecting the appropriate Electrode the last step, and maybe most critical, is to know how to read the identification of the electrode’s designation. This identification value consists of an “E” which stands for the electrode, followed by four to five digits.
The first two or three digits refer to the minimum tensile strength of the filler metal, e.g., we know that the filler metal E7018 is an electrode with a minimum tensile strength of 70,000psi given from the first 3 values “E70”. The next digit represents the position in which the electrode can be used.
For position, the value “1” indicates that the electrode is suitable for any position. The value of “2” indicates that the filler metal is molten metal and is so fluid that the electrode can only be used in the flat position for all welding types and the horizontal position for fillet welds. The value “4” indicates that the electrode is suitable for welding in a downhill progression.
The next value depends on which process you are using, however, in each case the last value indicates the Chemical/Operating Characteristics of the filler metal material. Below depicts examples of the Identification system for three welding processes (SMAW, FCAW, and GMAW).
Welding Electrode Identification
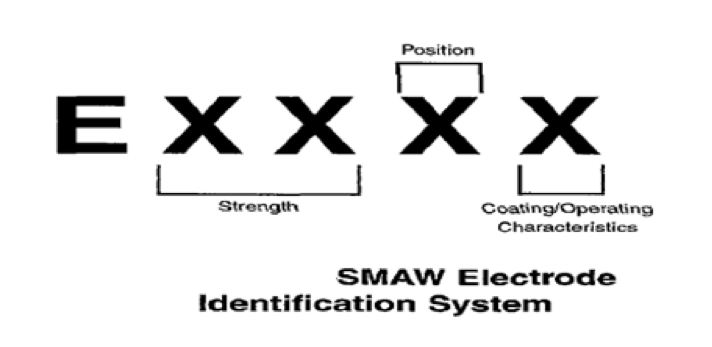
Matching filler metals to base metals is one of the most important factors in welding. Knowing and understanding this information will increase the safety during implementation as well as increase safety of the product constructed over the years of use.
Be safe and match appropriately. Check out ProWrite, a welding documentation software that will help with this step and many more of your welding needs.
Leave a Comment