Why would a designer need to consider alternate methods that might apply in producing an ASME compliant pressure vessel design? What are the options available, where do I find them and when do they apply? These are just some of the questions that I aim to address in this post.
Before I reveal when and where to use a specific method, perhaps I should first offer a couple of example methods:
- The Design by Rule (DBR) approach is your typical design methodology, which can be found in the ASME Boiler and Pressure Vessel codebooks in Section VIII, Part 4 for Division 2, and various Pressure Vessel References.
- The Design by Analysis (DBA) method, typically involves Finite Element Analysis (FEA) that requires a special understanding of the physics and methods of analysis proposal. Part 5 of Section VIII Division 2 of the ASME BPVC books provides extensive requirements for applying DBA.
Why would a designer need to consider both in a pressure vessel design?
Well, there are multiple reasons. In many cases, the DBR method’s scope is too restrictive for an aspect of the vessel design that still needs to be considered. In other cases, it may be to supplement the DBR method to check things like cycle life and secondary stresses that may not be considered in the root method.
In this scenario, a designer’s life is going to be made easier, if given access to tools that take advantage of both methods and can complement one another to produce a better result with less effort for the designer.
With 30+ years of software evolution in the field of Pressure Vessel Design and Prototyping, offering the assurance of DBR methods kept updated to the latest ASME Section VIII code, the team at CEI have continued to search for ways to deliver greater value to its loyal customer base.
A high-value way to achieve this aim is to establish quality integrations1 between CEI’s DesignCalcs system, and 3rd party developed PVPT design suite of products, such as NozzlePRO from Paulin Research Group for Finite Element Analysis, which extend the quality of the Vessel Designs produced and allow a designer to exploit both DBR and DBA methods.
CEI has, in this initial integration, released a limited set of features to use NozzlePRO, along with our other PVPT design suite of products, with nozzles that clients have already designed. If you are a current customer of PRG and use NozzlePRO, you can immediately analyze any nozzle designed in DesignCalcs with a shell host, simply by hitting the drop-down menu option during a user session to run the NozzlePRO export.
Here are the steps on how to do this:
- Set your NozzlePRO path:
- Go into a Nozzle design with a shell host and press the NozzlePRO button:
- Wait for NozzlePRO to do its magic:
- Review your output in the browser:
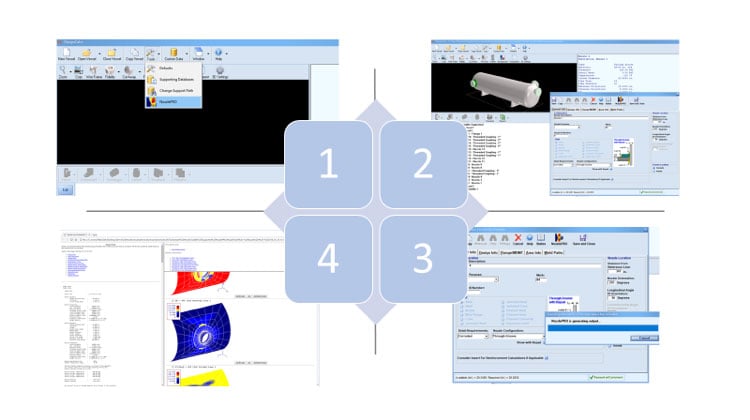
Note¹ “System integration is defined in information technology as the process of linking together different computing systems and software applications physically or functionally, to act as a coordinated whole.” Definition from Wikipedia
The key benefits of using DesignCalcs integration and NozzlePRO include:
- Seamlessly add checks for secondary stresses not natively considered in nozzle reinforcement methods.
- No fatigue? What about the basic cycle per day check for twenty years? It’s automatic.
- Already a common customer? No longer worry about making the mistake of forgetting to corrode your dimensions in NozzlePRO or accidentally picking a different pipe spec.
DesignCalcs provides a rich array of capabilities to the user, with an embedded library of industry data and proven methodologies that make ASME BPVC Section VIII pressure vessel design compliance easier than ever before! Now with the release of the NozzlePRO integration, a user can perform FEA directly on the same design session data.
As well, if you would like to learn more about how to increase welding process efficiency watch our latest webinar that industry expert Antonio Howard presented!
Leave a Comment